
blackbox use cases or prototype field tests by automotive OEMs. OBD2 loggers: Used to log OBD2 data from a car to an SD card - ideal for e.g. Further, CAN interfaces that support OBD2 requests can be useful as part of reverse engineering

OBD2 interfaces are typically used in advanced car diagnostics and OEM vehicle development.
Obd2 reader altima Pc#
OBD2 interfaces: Provide real-time OBD2 data to a PC via USB streaming. Personal driving behavior and vehicle health. The purpose of an OBD2 bluetooth dongle is typically to monitor Typically OBDII bluetooth dongles are low cost and easy-to-use, though also limited in terms of their usability outside the bluetooth-to-app visualization purpose.
Obd2 reader altima code#
Variants as simple car code readers for self-diagnosing their car health.īluetooth OBD2 dongles: Many OBD2 bluetooth dongles exist, which let you view car data directly on your smartphone via an app. Various types exist and some private persons use low cost An OBD2 scan tool is typically used in diagnosing vehicle issues e.g. OBD2 scanners: Used as car diagnostic tools in static reading/clearing of DTCs by e.g. Note that the last data byte (after Dh) is not used.īelow we outline the most common OBD2 analyzer categories: RPM (PID 0C), the formula is (256*A + B) / 4.Ī, B, C, D: These are the data bytes in HEX, which need to be converted to decimal form before they are used in the PID formula calculations. simply A, meaning that the A data byte (which is in HEX) is converted to decimal to get the km/h converted value (i.e. Each PID has a description and some have a specified min/max and conversion formula.
Obd2 reader altima full#
For the full list, check out our OBD2 PID overview. PID: For each mode, a list of standard OBD2 PIDs exist - e.g. show or clear stored diagnostic trouble codes and show freeze frame data. used for looking at real-time vehicle speed, RPM etc. There are 10 modes as described in the SAE J1979 OBD2 standard. For responses the 0 is replaced by 4 (i.e. Mode: For requests, this will be between 01-0A. For the Vehicle Speed example, it is 02 for the request (since only 01 and 0D follow), while for the response it is 03 as both 41, 0D and 32 follow. Length: This simply reflects the length in number of bytes of the remaining data (03 to 06). Note that 7E8 will typically be where the main engine or ECU responds at. Identifier: For OBD2 messages, the identifier is standard 11-bit and used to distinguish between "request messages" (ID 7DF) and "response messages" (ID 7E8 to 7EF). ISO 14229: This describes UDS communication in detail This standard is important as it forms the basis for Unified Diagnostic Services (UDS) communication, which relies on sending multiframe CAN data packets.
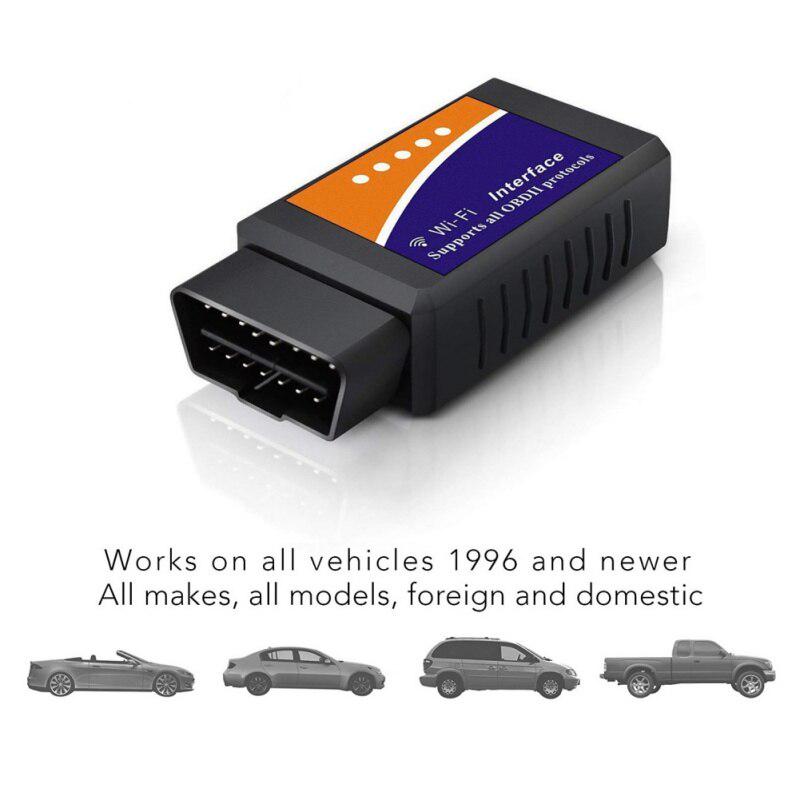
Obd2 reader altima how to#
how to send data packets exceeding 8 bytes via CAN bus. ISO 15765-2: The ISO-TP standard describes the 'Transport Layer', i.e. ISO 11898: This standard describes the CAN bus data link layer and physical layer, serving as the basis for OBD2 communication in most cars today While OBD2 PID information is only available on-request by OBD2 test equipment, the J1939 protocol is used in most heavy-duty vehicles as the basic means for communicating CAN traffic. SAE J1939: The J1939 standard describes the data protocol used for heavy-duty vehicle communication. Vehicle OEMs may also decide to implement additional proprietary OBD2 PIDs beyond those outlined by the SAE J1979 standard. Implement in cars (though they are not required to do so). It also includes a list of standardized public OBD2 parameter IDs (OBD2 PIDs) that automotive OEMs may SAE J1979: The SAE J1979 standard describes the methods for requesting diagnostic information via the OBD2 protocol. Location and access to the OBD2 connector. The standard describes both the vehicle OBD2 connector and the connector used by the external test equipment (e.g.

SAE J1962: This standard defindes the physical connector used for the OBD2 interfacing, i.e. Below we list some of the most relevant SAE/ISO standards related to OBD2:
